Der C30SE Motor
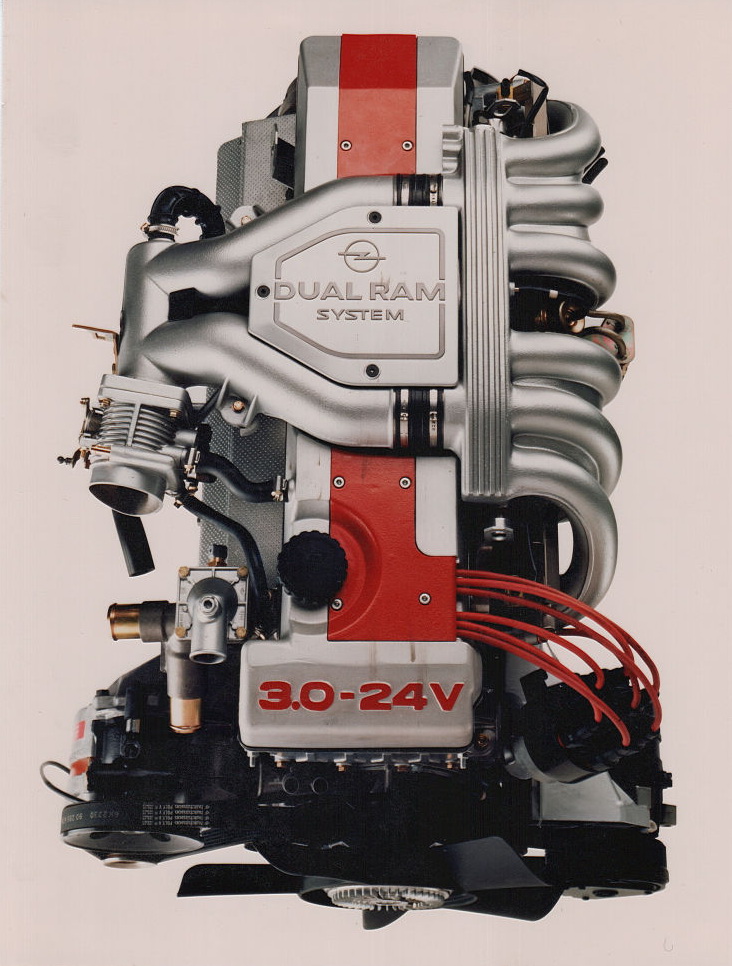
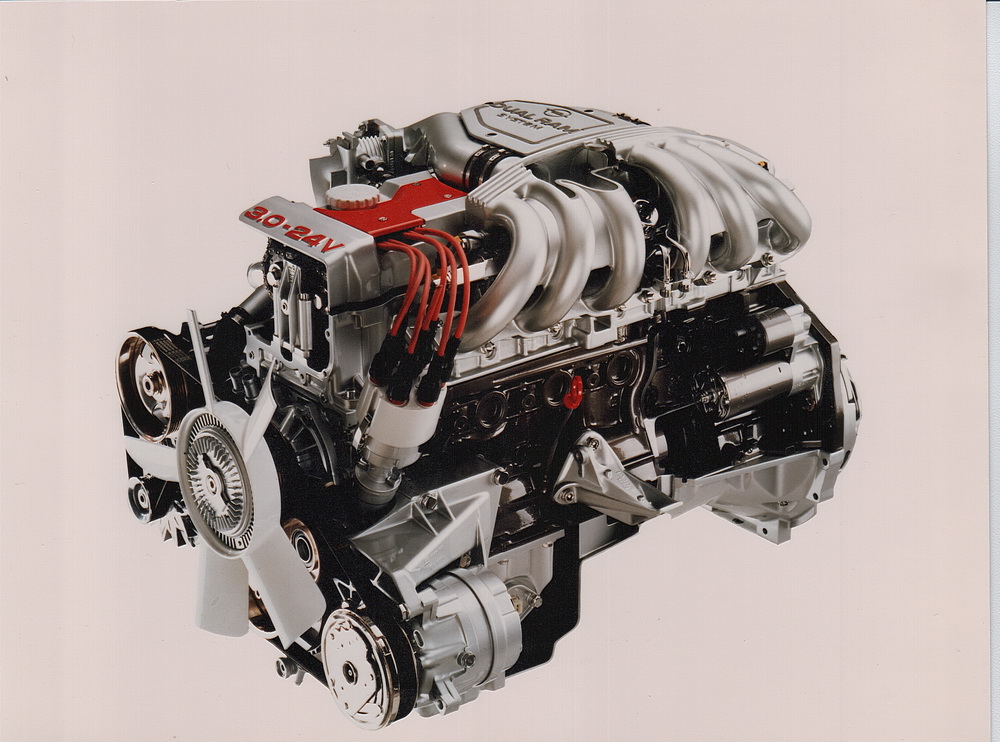
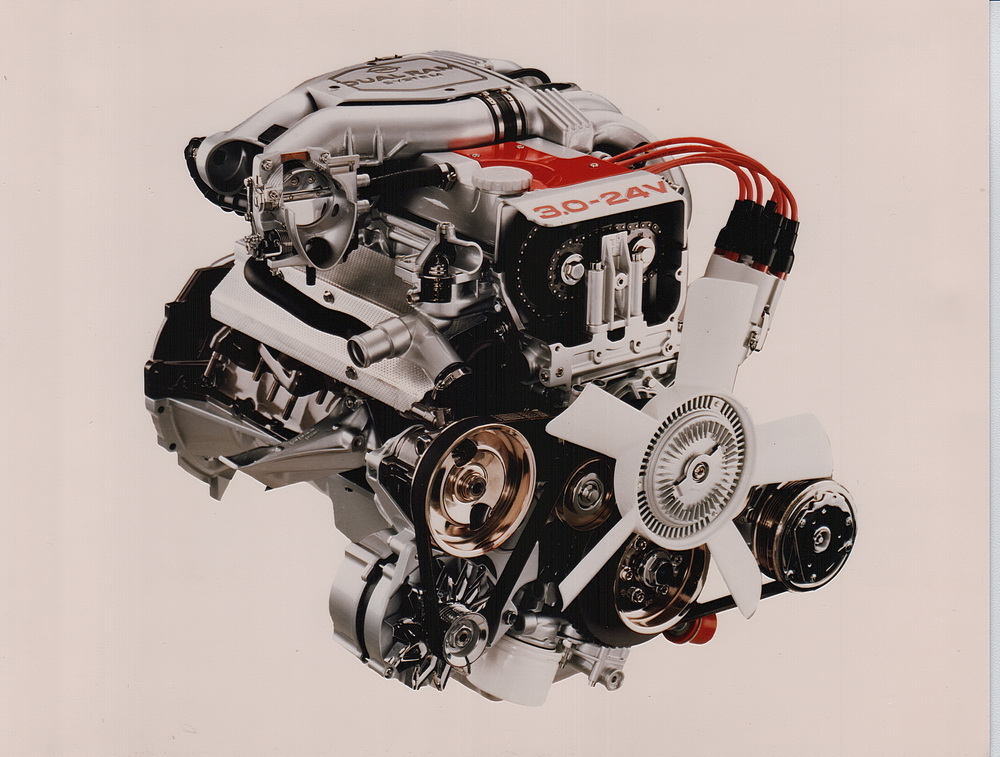
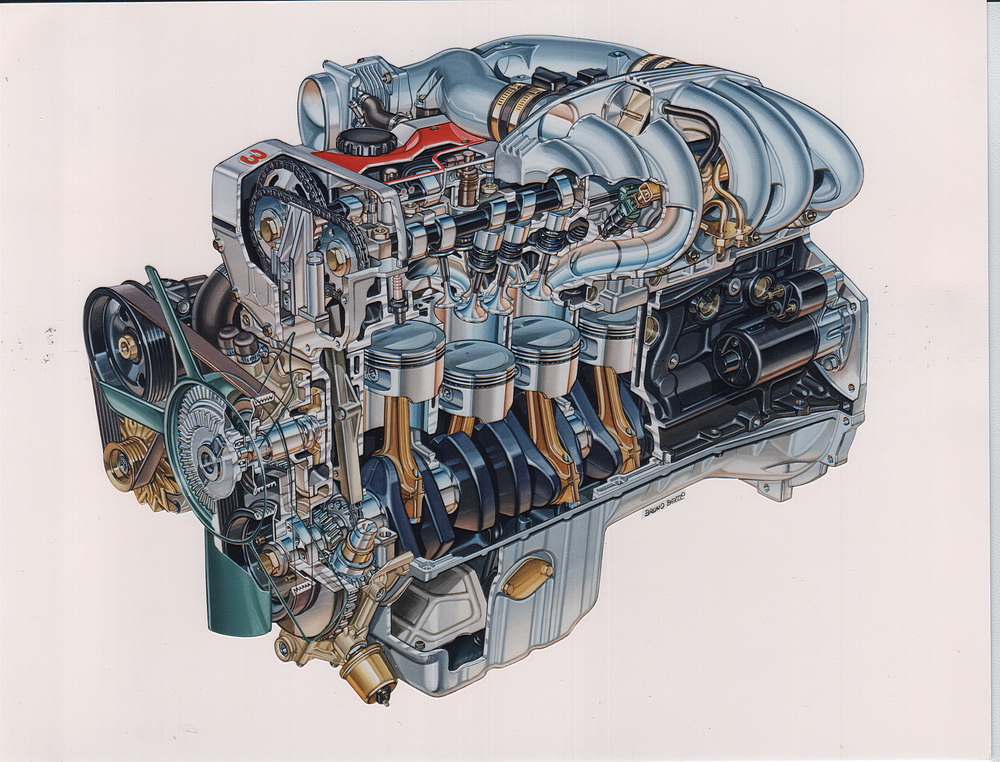
- Produktionsdatum 10/89 bis 5/93 ( Als C40SE : 09/90 bis 05/93 von Irmscher und Mantzel)
- Wassergekühlter Reihen Sechszylinder
- Zwei Oben Liegende Nockenwellen - Vierventiler
- Elektronische Kraftstoffeinspritzung - Motronic 1.5
- Schaltsaugrohr (DUAL-RAM)
- Leistung 150 KW / 204 PS bei 6000 u/min1 (Als C40SE 200 KW / 272 PS bei 5800 u/min1 )
> - Hubraum 2969 ccm3 ( 95mm x 69,8mm ) (Als C40SE : 3983 ccm3 98mm x 88mm )
- Verdichtungsverhältnis 10,0:1
- Schräg hängende Ventile, Hydrostößel, 2 obenliegende Nockenwellen, 2 Ketten
- Drehmoment 270nm bei 3600 u/min1 ( Als C40SE 395nm bei 3300 u/min1 )
- Klopfsensoren für Benzi 91/95 Oktan
- Nockenwellenantrieb über Steuerkette
- Ölfüllmenge mit Ölkühler 5,5 Liter
Fahrwerte Omega A 3000 24V
- Beschleunigung von 0-100km/h: 7,9s** ( Angabe Opel : 9,0s )
- Höchstgeschwindigkeit: 246km/h** ( Angabe Opel : 240 km/h )
- Verbrauch: 12,5 Liter/100km**
**Messwerte einer Autozeitschrift
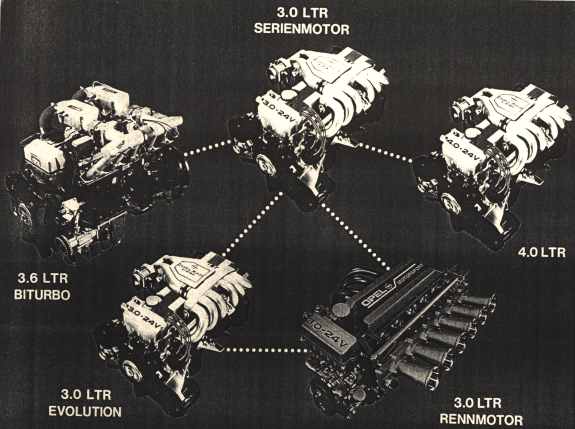
Der Rennmotor
Das Bild zeigt den Serienmotor und den Evolutionsmotor als Basis für den Rennmotor sowie die beiden hubraumgrößeren Entwicklungen, den 3,6-l-Biturbo- und den 4,0-l-Saugmotor.
Geometrische Hauptdaten dieser OPEL-Motorenbaureihe mit einem Zylinderabstand von 105mm werden in der folgenden Tabelle dargestellt.
Der Standardhub von 69,8mm wird bei anderen Kurbelwellen auf 85 mm beim 3,6-l- und auf 88mm beim 4,0-l-Motor vergrößert.
Die Grundbohrung von 95mm ist beim 4,0-l-Motor auf 98mm vergrößert, während beim Rennmotor 95,4mm Bohrung zur Ausnutzung der Hubraumgrenze von 3-l benötigt werden.
Der Abstand zwischen 2 Zylindern beträgt selbst beim 4,0-l-Motor noch sichere 7mm. Alle Motoren dieser Reihe sind Kurzhubmotoren.
Die Leistungs- und Drehmomentdaten lassen in der folgenden Tabelle die unterschiedlichen Zielrichtungen der Entwicklungen erkennen.
Insbesondere der 4,0-l-Motor ist bei ausreichender Leistung für hohes Drehmoment schon im unteren Drehzahlbereich ausgelegt.
Der für den Serienmotor neu entwickelte Zylinderblock mit hoher Steifigkeit wurde den erhöhten Beanspruchungen des Rennmotors angepaßt:
1. Die Schottwände wurden von einer 5mm dicken Rippe zu einer massiven Wand ausgebildet, damit die Hauptlagerstühle nicht ausbrechen.
2. Aus gleichem Grund sind die Hauptlagerdeckel durch modifizierte Lagerdeckel des aufgeladenen 2,3-l-Vierzylinder-Dieselmotors ersetzt.
Die Verschraubung der Lagerdeckel erfolgt mit längeren Schrauben und mit der Drehwinkel-Anziehmethode.
3. Die Radien der Pulsationsfenster sind aus Festigkeitsgründen vergrößert.
Die Kühlung des Brennraums und der unmittelbar angrenzenden Bereiche wurde überarbeitet.
Die im nachfolgenden Bild gezeigte Oberseite des Motorblockes weist eine um jeden Zylinder laufende, wasserführende Ringnut auf,
die zwischen den Zylindern als gerade Verbindungsnut verläuft.
Neben dem Kühleffekt wird auch eine bessere Druckverteilung für die Brennraumeinfassung der Zylinderkopfdichtung erreicht, die Dichtung entspricht der des Bi-Turbomotors.
Zur Kühlung des Kolbenbodens ist für jeden Zylinder ein Spritzventil am Hauptölkanal angeordnet.
Dieses öffnet ab einem Öldruck von 1,5 bar und spritzt je nach Öldruck zwischen 0,6 und 2,1 Liter Öl pro Minute unter den Kolbenboden.
der Volumenstrom mit Toleranzfeld ist in Abhängigkeit vom Öldruck im folgenden Bild dargestellt.
Da nach dem Reglement der Einsatz einer Trockensumpfschmierung nicht gestattet war, sorgen ein aufwendiger Ölhobel und Abschirmbleche dafür, das der Öldruckabfall beim Bremsen in akzeptabelen Grenzen bleibt.
Die Telemetriedaten im Bild zeigen die Beschleunigung des Fahrzeuges bis zum fünften Gang, die Bremsphase mit "Zwischengasgeben" und das Wiederbeschleunigen im zweiten Gang.
Neben den deutlich hervorgehobenen Linien für die Schieberposition, Drehzahl und Öldruck sind noch Lambda1 für Zylinder 1+2+3 und Lambda 2 für Zylinder 4+5+6, Kraftstoffdruck, Öffnungszeit der Einspritzventile und die Öltemperatur aufgeschrieben.
Der kurzzeitige Öldruckabfall auf 0,8 bar wird vom Motor verkraftet. Die neueste Ausführung der Ölwanne hat durch seitliche Ausbuchtungen ein größeres Ölvolumen, und ein Klappensystem sorgt dafür, daß nun der Öldruck nicht mehr unter 1,8 bar abfällt.
Der Kurbeltrieb weicht in allen Bauteilen vom Serienmotor ab.
Der Kolben ist ein geschmiedeter Kastenkolben und wiegt 321 g ( Serie 494 g).
Der Kolbenbolzen ist im Durchmesser reduziert, verkürzt und konisch aufgebohrt; Gewicht 85 g ( Serie 116 g).
Der schwimmend gelagerte Kolbenbolzen wird mit Drahtsprengringen gesichert. Die Kompressionsringe sind aus Sphäroguß, molybdänbeschichtet und in der ersten Nut 1,2mm, in der zweiten Nut 1,0mm hoch. Der als Schlauchfederring ausgebildete Ölabstreifer ist 2,5mm hoch. Letzte Entwicklungen befaßten sich mit der Reduktion der Reibbelastung durch Kolben mit nur zwei Kolbenringen.
Die aus 31 Cr Mo V9 geschmiedete Pleuelstange ist 10mm länger als das Serienpleuel. Hochfeste Schrauben aus Nimonic sichern die Lagerdeckel. Das Pleuel wiegt 630 g gegenüber 720 g der Serienausführung.
Das Pleuel und die niedrigen Kolbenringe ergeben bei unverändertem Hub der Kurbelwelle und serienmäßiger Blockhöhe die sehr niedrige Kolben-Kompressionshöhe von 27,5mm.
Bei Reihen-Sechszylinder-Rennmotoren stellt die lange Kurbelwelle das größte Problem dar. Hier muß ein guter Kompromiß zwischen hoher Drehsteifigkeit und erträglicher Hauptlagerbelastung gefunden werden. Mit einer neu konstruierten, geschmiedeten Kurbelwelle mit 8 um 180 Grad versetzten, anstatt der serienmäßig zwölf um 120 Grad versetzten Gegengewichten wurde der gewünschte Kompromiß erreicht.
Das nachfolgende Bild zeigt die errechneten Lagerbelastungen mit der neuartigen Kurbelwelle schraffiert. Eine weitere Reduzierung der Gegengewichtsmassen führt zu unvertretbaren Hauptlagerbelastungen, hier schwarz dargestellt.
Die Reduzierung der Gegengewichte ergab eine Gewichtsverminderung um 22% auf 23 kg gegenüber Serie von 29,5 kg. Die gemessenen Schwingungen am vorderen Ende der Kurbelwelle werden im Bild dargestellt. Aufgrund der gezeigten Meßwerte ist diese Kurbelwelle geeignet, Drehzahlen bis 10 000 U/min zu ertragen.
Der Zylinderkopf ist beim Serienmotor mit dem drehmomentsteigernden Dual-Ram-System ausgestattet, während der Rennmotor separate Einlaßtrichter hat. Im Fahrzeug werden diese von einer Airbox aus Kevlar überdeckt. Wie beim Serienmotor beträgt der Winkel zwischen Ein- und Auslassventilen 29 Grad, wobei die Einlassventile mit der Zylinderachse einen Winkel von 10 Grad bilden. Die Einlaßventile sind etwas vom Zylinderrand zur Zylindermitte gerückt. Dadurch ist zwar nicht der größtmögliche Ventildurchmesser realisiert worden, die Einströmverhältnisse in den Zylindern sind jedoch deutlich verbessert. Ventilhübe, Ventilerhebung, Spreizung, Überschneidung und Steuerzeiten beim Rennmotor weichen stark vom Serienmotor ab:
Um bei den größeren Ventilhüben und der relativ hohen Drehzahl die Nockenbelastung sicher zu beherrschen, wurde der Tassenstößeldurchmesser von 32mm auf 35mm vergrößert. Trotzdem ist damit gegenüber der Serie eine Massenreduzierung von 31% verbunden, nicht zuletzt deshalb, weil die hydraulischen Tassenstößel durch mechanische ersetzt wurden. Ein- und Auslassventile ( Werkstoff: Nimonic, natriumgefüllt) sind im Tellerdurchmesser je um 1mm gegenüber dem Serienmotor vergrößert.
Die Gestaltung des Brennraums ist eine sehr diffizile, aber lohnende Aufgabe. Hier nimmt der Entwickler den größten Einfluß auf den Verbrennungsablauf und die gerade bei hohen Drehzahlen nötige schnelle Energieumsetzung. Brennverlauf und Brennfunktion zeigt das folgende Bild. Dabei sollte berücksichtigt werden, das 1 Grad Kurbelwinkel bei 6000 U/min in 27 mykro-Sekunden und bei 8800 U/min in 18 mykro-Sekunden durchlaufen wird.
Das p-V Diagramm im nächsten Bild ist jeweils bei Nennleistung aufgenommen und aus 200 Zyklen gemittelt. Wegen der zyklischen Schwankungen sind maximale Zünddrücke von über 100 bar, aber auch Ausreißer von nur 65 bar gemessen worden. In einer Vergleichmäßigung liegt noch viel Entwicklungsarbeit.
Im Vergleich zum Serienmotor hat der Rennmotor einen überarbeiteten Brennraum. Auf ausgeprägte Quetschflächen wurde wegen der Turbulenzen bei hohen Drehzahlen verzichtet. Auf möglichst günstige Ein- und Auslassströmungsbedingungen hingegen großer Wert gelegt.
Die Form des Kolbenbodens als abschließendes Element des Brennraumes kann bei Verdichtungsverhältnissen von etwa 12:1 zu einem Problem werden. Große Überschneidungen, Ventilhübe, Ventildurchmesser und große Ventilwinkel führen oft zu stark zerklüfteten Kolbenböden. Beim OPEL-Sechszylinder-Rennmotor wurde wegen des relativ kleinen Ventilwinkels und der in Richtung Zylindermitte gerückten Einlaßventile bei genügend großen Ventilhüben jedoch ein guter Kompromiß gefunden.
Die vorteilhafte Auslegung dieses Brennraumes zeigt sich auch darin, daß nahezu im gesamten Drehzahlbereich der Motor mit optimalem Zündzeitpunkt betrieben werden kann. Zur Erhöhung des Gasdurchsatzes wurden auch die Ein- und Auslaßkanäle gegenüber der Serie modifiziert. Auf der Fließbank sind die Luftdurchsatzwerte dieser Kanäle im Vergleich zum Serienmotor und zu Konkurrenzmotoren gleichen Zylindervolumens ermittelt worden.
Im Bild oberhalb ist der Einlaßkanal-Luftdurchsatz in Abhängigkeit bei konstanter Druckdifferenz dargestellt. Der Auslaßkanal wird in Ausströmrichtung bei einer Druckdifferenz von 650 mbar gemessen.
Zur Füllungsregelung wird ein Flachschieber mit einer Durchlaßöffnung von 47mm benutzt. Der Flachschieber läuft auf Nadelflachkäfigen und wird mit einem Winkelhebel betätigt, auf dessen Drehachse ein Potentiometer die Schieberposition bzw. den Lastzustand signalisiert.
Auf der Auslaßseite sind die Krümmer der Serie (Grauguß) durch einen in den Rohrlängen genau abgestimmten geschweißten Stahlrohrkrümmer aus warmfesten Werkstoff ersetzt. Wie beim Serienmotor werden die Zylinder 1+2+3 und 4+5+6 jeweils in ein Rohr zusammengeführt.
Um die Abgaswerte in einem vom Reglement definierten Meßpunkt und die Geräuschvorschriften zu erfüllen, werden die Abgasrohre in einen Katalysator und dann durch zwei Absorptionsschalldämpfer geführt.
Vorschrift lt. Reglement:
Abgas: n = 5000 U/min ( ohne Last) CO = 0,5 Vol.-% (+0,2 Vol.-% Meßtoleranz)
Geräusch = ONS-Nahfeldmessung 98 dB(A) +2 dB(A) Toleranz
Der Katalysator erhöht den Abgasgegendruck und mindert somit die Leistung. Die Unterschiede für die Abgasanlage mit und ohne Katalysator zeigt das folgende Bild:
Zum Einsatz kommt die BOSCH Rennmotronic M 1.8, diese Anlage regelt Zündung und Einspritzung zylinderselektiv bis zu höchsten Drehzahlen. Fünfzehn parallel arbeitende Rechner im Steuergerät sorgen für die nötige Schnelligkeit. Pro Zylinder werden zwei Einspritzventile mit last- und drehzahlabhängigen unterschiedlichen Öffnungszeiten betrieben.
Im Gegensatz zum Serienmotor, der mit einem Zündverteiler ausgerüstet ist, hat der Rennmotor eine ruhende Hochspannungsverteilung. Die Zylinder-1.-Erkennung befindet sich an der Stelle des bisherigen Zündverteilers. Drehzahlinformation und O.T.-Position werden an der dafür günstigsten Stelle, dem Schwungrad, abgenommen.
Die Leistungsentwicklung wurde in 3 Phasen geplant:
Phase 1 : 265 kW bei 8000 U/min war im Februar 1990 abgeschlossen. Die Leistung wurde mit dem ersten Prototyp erreicht.
Phase 2 : 295 kW bei 8600 U/min wurde im August 1990 erreicht.
Phase 3 : etwa 310 kW bei 9200 U/min lief seit Anfang 1991 und wurde bald fertiggestellt.
Schon bei der Entwicklung des OPEL-Sechszylinder-Vierventilmotors für den Omega 3000-24V wurde ein späterer Renneinsatz nicht ausgeschlossen. Die günstigen Voraussetzungen des Basismotors, auch im Hinblick auf extrem hohe Literleistung, bestätigten sich während der Entwicklung zum Rennmotor. Es wurde besonders auf den Kurbeltrieb geachtet, um die für den Rennbetrieb notwendigen hohen Drehzahlen bis 10 000 U/min realisieren zu können. Nach bisherigen Erkenntnissen scheint mit dem Leistungsziel Phase 3, d.h. 310 kW das Leistungspotenzial immer noch nicht ganz ausgeschöpft zu sein.
Artikel aus der MZT, Ausgabe 52 von 1991 Alle Urheberrechte bei den Verfassern Verfasser: Prof. Dr.-Ing. Fritz Indra Dipl.-Ing. Manfred Tholl Senator-Monza.de
Geometrische Hauptdaten dieser OPEL-Motorenbaureihe mit einem Zylinderabstand von 105mm werden in der folgenden Tabelle dargestellt.
Der Standardhub von 69,8mm wird bei anderen Kurbelwellen auf 85 mm beim 3,6-l- und auf 88mm beim 4,0-l-Motor vergrößert.
Die Grundbohrung von 95mm ist beim 4,0-l-Motor auf 98mm vergrößert, während beim Rennmotor 95,4mm Bohrung zur Ausnutzung der Hubraumgrenze von 3-l benötigt werden.
Der Abstand zwischen 2 Zylindern beträgt selbst beim 4,0-l-Motor noch sichere 7mm. Alle Motoren dieser Reihe sind Kurzhubmotoren.

Die Leistungs- und Drehmomentdaten lassen in der folgenden Tabelle die unterschiedlichen Zielrichtungen der Entwicklungen erkennen.
Insbesondere der 4,0-l-Motor ist bei ausreichender Leistung für hohes Drehmoment schon im unteren Drehzahlbereich ausgelegt.

Der für den Serienmotor neu entwickelte Zylinderblock mit hoher Steifigkeit wurde den erhöhten Beanspruchungen des Rennmotors angepaßt:
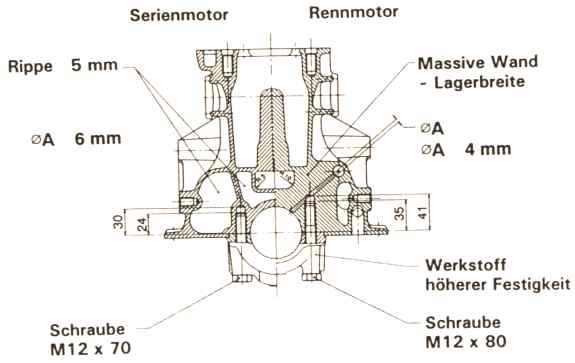
1. Die Schottwände wurden von einer 5mm dicken Rippe zu einer massiven Wand ausgebildet, damit die Hauptlagerstühle nicht ausbrechen.
2. Aus gleichem Grund sind die Hauptlagerdeckel durch modifizierte Lagerdeckel des aufgeladenen 2,3-l-Vierzylinder-Dieselmotors ersetzt.
Die Verschraubung der Lagerdeckel erfolgt mit längeren Schrauben und mit der Drehwinkel-Anziehmethode.
3. Die Radien der Pulsationsfenster sind aus Festigkeitsgründen vergrößert.
Die Kühlung des Brennraums und der unmittelbar angrenzenden Bereiche wurde überarbeitet.
Die im nachfolgenden Bild gezeigte Oberseite des Motorblockes weist eine um jeden Zylinder laufende, wasserführende Ringnut auf,
die zwischen den Zylindern als gerade Verbindungsnut verläuft.
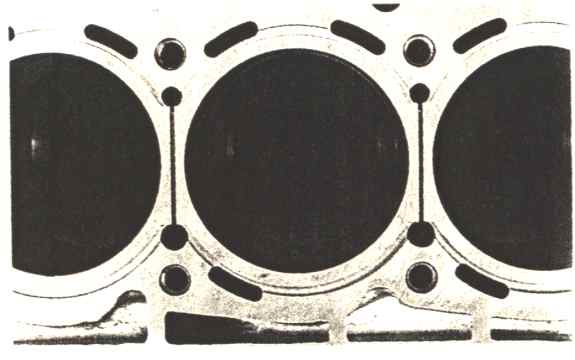
Neben dem Kühleffekt wird auch eine bessere Druckverteilung für die Brennraumeinfassung der Zylinderkopfdichtung erreicht, die Dichtung entspricht der des Bi-Turbomotors.
Zur Kühlung des Kolbenbodens ist für jeden Zylinder ein Spritzventil am Hauptölkanal angeordnet.
Dieses öffnet ab einem Öldruck von 1,5 bar und spritzt je nach Öldruck zwischen 0,6 und 2,1 Liter Öl pro Minute unter den Kolbenboden.
der Volumenstrom mit Toleranzfeld ist in Abhängigkeit vom Öldruck im folgenden Bild dargestellt.
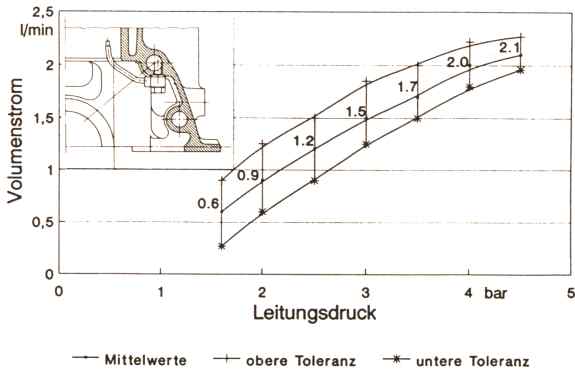
Da nach dem Reglement der Einsatz einer Trockensumpfschmierung nicht gestattet war, sorgen ein aufwendiger Ölhobel und Abschirmbleche dafür, das der Öldruckabfall beim Bremsen in akzeptabelen Grenzen bleibt.
Die Telemetriedaten im Bild zeigen die Beschleunigung des Fahrzeuges bis zum fünften Gang, die Bremsphase mit "Zwischengasgeben" und das Wiederbeschleunigen im zweiten Gang.
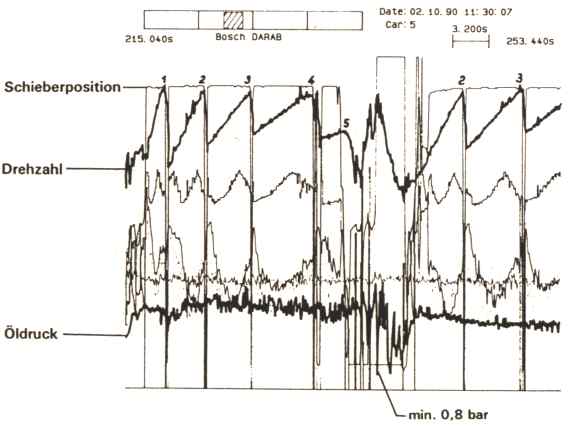
Neben den deutlich hervorgehobenen Linien für die Schieberposition, Drehzahl und Öldruck sind noch Lambda1 für Zylinder 1+2+3 und Lambda 2 für Zylinder 4+5+6, Kraftstoffdruck, Öffnungszeit der Einspritzventile und die Öltemperatur aufgeschrieben.
Der kurzzeitige Öldruckabfall auf 0,8 bar wird vom Motor verkraftet. Die neueste Ausführung der Ölwanne hat durch seitliche Ausbuchtungen ein größeres Ölvolumen, und ein Klappensystem sorgt dafür, daß nun der Öldruck nicht mehr unter 1,8 bar abfällt.
Der Kurbeltrieb weicht in allen Bauteilen vom Serienmotor ab.
Der Kolben ist ein geschmiedeter Kastenkolben und wiegt 321 g ( Serie 494 g).
Der Kolbenbolzen ist im Durchmesser reduziert, verkürzt und konisch aufgebohrt; Gewicht 85 g ( Serie 116 g).
Der schwimmend gelagerte Kolbenbolzen wird mit Drahtsprengringen gesichert. Die Kompressionsringe sind aus Sphäroguß, molybdänbeschichtet und in der ersten Nut 1,2mm, in der zweiten Nut 1,0mm hoch. Der als Schlauchfederring ausgebildete Ölabstreifer ist 2,5mm hoch. Letzte Entwicklungen befaßten sich mit der Reduktion der Reibbelastung durch Kolben mit nur zwei Kolbenringen.
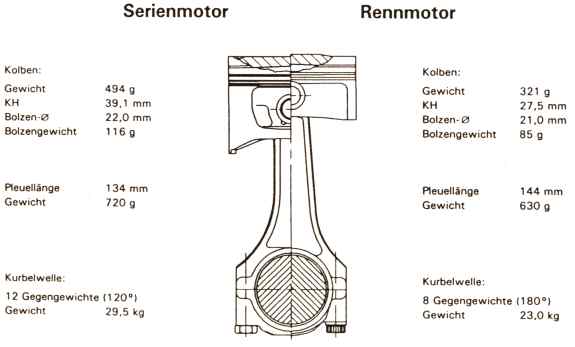
Die aus 31 Cr Mo V9 geschmiedete Pleuelstange ist 10mm länger als das Serienpleuel. Hochfeste Schrauben aus Nimonic sichern die Lagerdeckel. Das Pleuel wiegt 630 g gegenüber 720 g der Serienausführung.
Das Pleuel und die niedrigen Kolbenringe ergeben bei unverändertem Hub der Kurbelwelle und serienmäßiger Blockhöhe die sehr niedrige Kolben-Kompressionshöhe von 27,5mm.
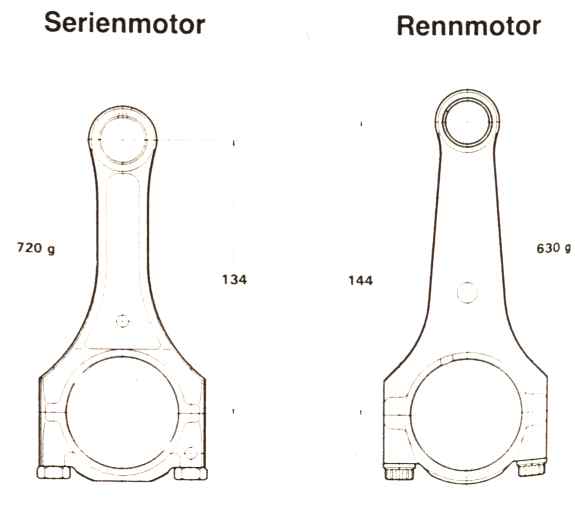
Bei Reihen-Sechszylinder-Rennmotoren stellt die lange Kurbelwelle das größte Problem dar. Hier muß ein guter Kompromiß zwischen hoher Drehsteifigkeit und erträglicher Hauptlagerbelastung gefunden werden. Mit einer neu konstruierten, geschmiedeten Kurbelwelle mit 8 um 180 Grad versetzten, anstatt der serienmäßig zwölf um 120 Grad versetzten Gegengewichten wurde der gewünschte Kompromiß erreicht.
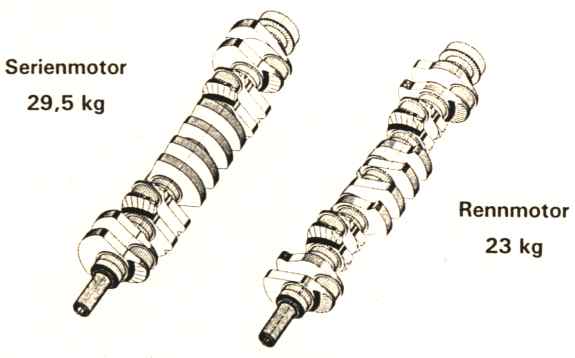
Das nachfolgende Bild zeigt die errechneten Lagerbelastungen mit der neuartigen Kurbelwelle schraffiert. Eine weitere Reduzierung der Gegengewichtsmassen führt zu unvertretbaren Hauptlagerbelastungen, hier schwarz dargestellt.
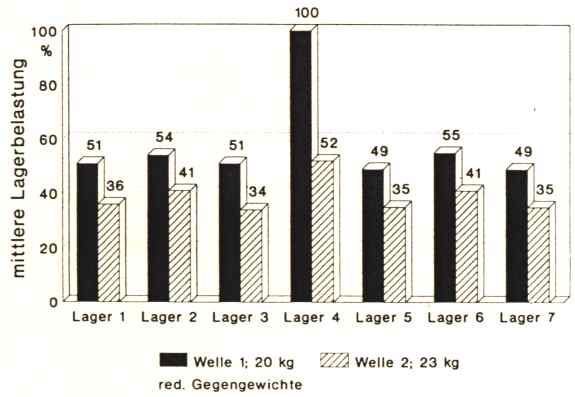
Die Reduzierung der Gegengewichte ergab eine Gewichtsverminderung um 22% auf 23 kg gegenüber Serie von 29,5 kg. Die gemessenen Schwingungen am vorderen Ende der Kurbelwelle werden im Bild dargestellt. Aufgrund der gezeigten Meßwerte ist diese Kurbelwelle geeignet, Drehzahlen bis 10 000 U/min zu ertragen.
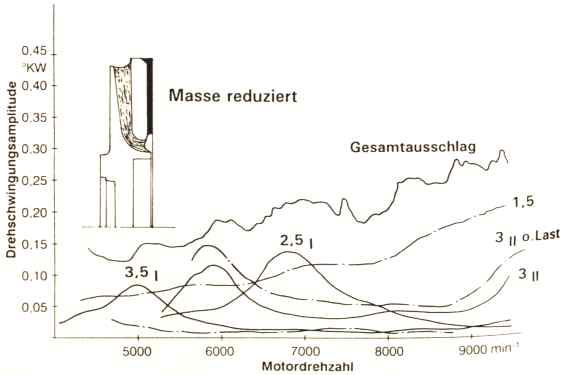
Der Zylinderkopf ist beim Serienmotor mit dem drehmomentsteigernden Dual-Ram-System ausgestattet, während der Rennmotor separate Einlaßtrichter hat. Im Fahrzeug werden diese von einer Airbox aus Kevlar überdeckt. Wie beim Serienmotor beträgt der Winkel zwischen Ein- und Auslassventilen 29 Grad, wobei die Einlassventile mit der Zylinderachse einen Winkel von 10 Grad bilden. Die Einlaßventile sind etwas vom Zylinderrand zur Zylindermitte gerückt. Dadurch ist zwar nicht der größtmögliche Ventildurchmesser realisiert worden, die Einströmverhältnisse in den Zylindern sind jedoch deutlich verbessert. Ventilhübe, Ventilerhebung, Spreizung, Überschneidung und Steuerzeiten beim Rennmotor weichen stark vom Serienmotor ab:
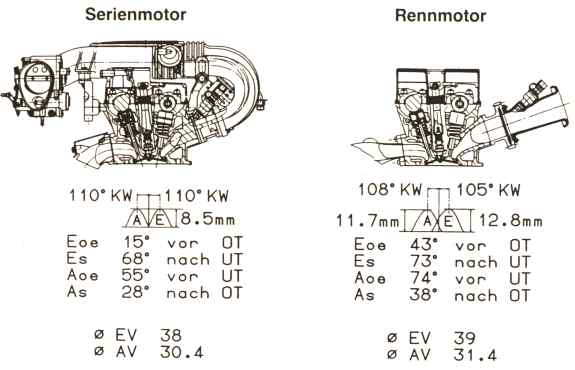
Um bei den größeren Ventilhüben und der relativ hohen Drehzahl die Nockenbelastung sicher zu beherrschen, wurde der Tassenstößeldurchmesser von 32mm auf 35mm vergrößert. Trotzdem ist damit gegenüber der Serie eine Massenreduzierung von 31% verbunden, nicht zuletzt deshalb, weil die hydraulischen Tassenstößel durch mechanische ersetzt wurden. Ein- und Auslassventile ( Werkstoff: Nimonic, natriumgefüllt) sind im Tellerdurchmesser je um 1mm gegenüber dem Serienmotor vergrößert.
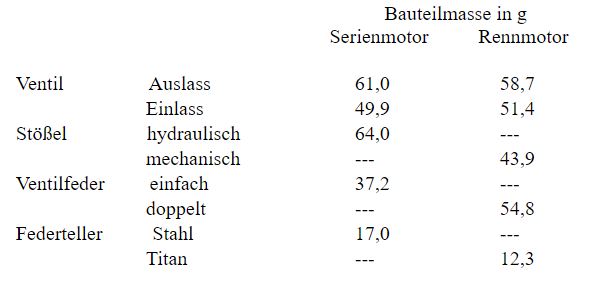
Die Gestaltung des Brennraums ist eine sehr diffizile, aber lohnende Aufgabe. Hier nimmt der Entwickler den größten Einfluß auf den Verbrennungsablauf und die gerade bei hohen Drehzahlen nötige schnelle Energieumsetzung. Brennverlauf und Brennfunktion zeigt das folgende Bild. Dabei sollte berücksichtigt werden, das 1 Grad Kurbelwinkel bei 6000 U/min in 27 mykro-Sekunden und bei 8800 U/min in 18 mykro-Sekunden durchlaufen wird.
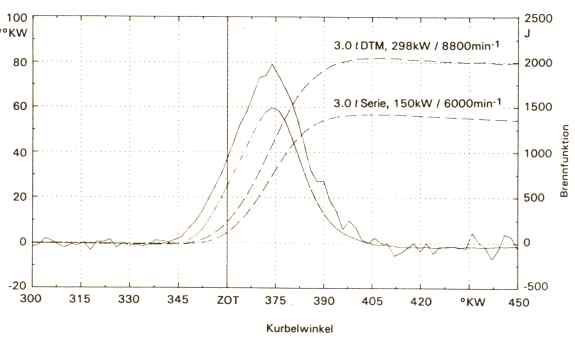
Das p-V Diagramm im nächsten Bild ist jeweils bei Nennleistung aufgenommen und aus 200 Zyklen gemittelt. Wegen der zyklischen Schwankungen sind maximale Zünddrücke von über 100 bar, aber auch Ausreißer von nur 65 bar gemessen worden. In einer Vergleichmäßigung liegt noch viel Entwicklungsarbeit.
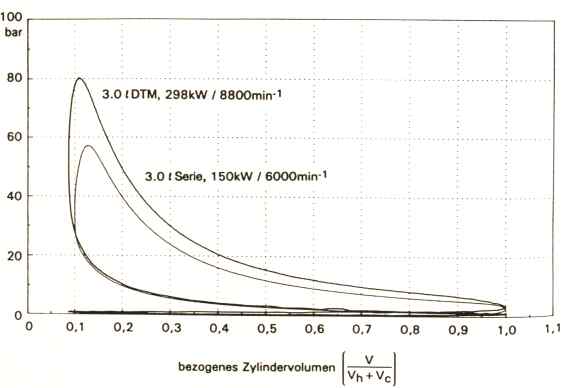
Im Vergleich zum Serienmotor hat der Rennmotor einen überarbeiteten Brennraum. Auf ausgeprägte Quetschflächen wurde wegen der Turbulenzen bei hohen Drehzahlen verzichtet. Auf möglichst günstige Ein- und Auslassströmungsbedingungen hingegen großer Wert gelegt.
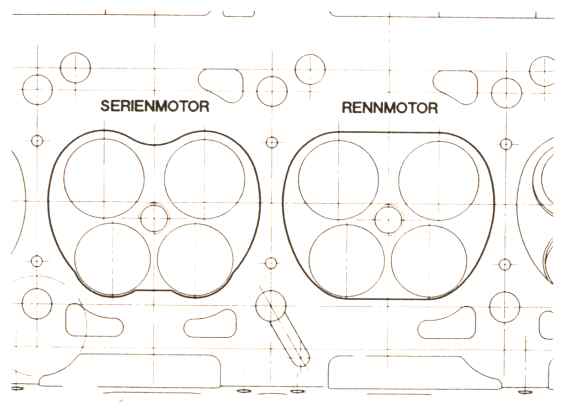
Die Form des Kolbenbodens als abschließendes Element des Brennraumes kann bei Verdichtungsverhältnissen von etwa 12:1 zu einem Problem werden. Große Überschneidungen, Ventilhübe, Ventildurchmesser und große Ventilwinkel führen oft zu stark zerklüfteten Kolbenböden. Beim OPEL-Sechszylinder-Rennmotor wurde wegen des relativ kleinen Ventilwinkels und der in Richtung Zylindermitte gerückten Einlaßventile bei genügend großen Ventilhüben jedoch ein guter Kompromiß gefunden.
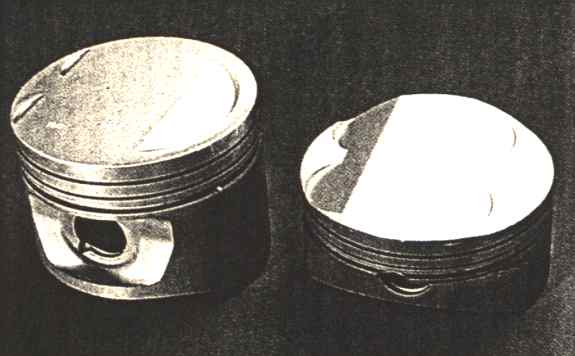
Die vorteilhafte Auslegung dieses Brennraumes zeigt sich auch darin, daß nahezu im gesamten Drehzahlbereich der Motor mit optimalem Zündzeitpunkt betrieben werden kann. Zur Erhöhung des Gasdurchsatzes wurden auch die Ein- und Auslaßkanäle gegenüber der Serie modifiziert. Auf der Fließbank sind die Luftdurchsatzwerte dieser Kanäle im Vergleich zum Serienmotor und zu Konkurrenzmotoren gleichen Zylindervolumens ermittelt worden.
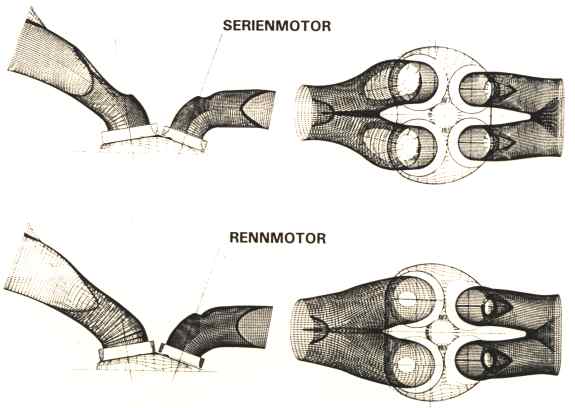
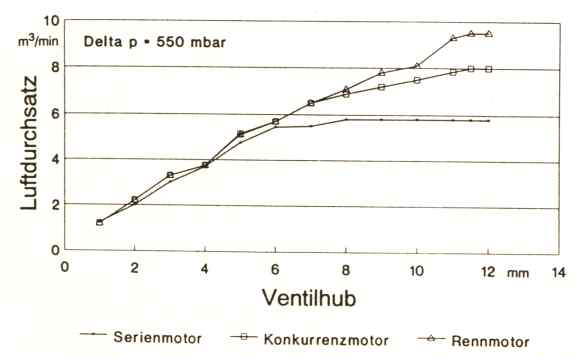
Im Bild oberhalb ist der Einlaßkanal-Luftdurchsatz in Abhängigkeit bei konstanter Druckdifferenz dargestellt. Der Auslaßkanal wird in Ausströmrichtung bei einer Druckdifferenz von 650 mbar gemessen.
Zur Füllungsregelung wird ein Flachschieber mit einer Durchlaßöffnung von 47mm benutzt. Der Flachschieber läuft auf Nadelflachkäfigen und wird mit einem Winkelhebel betätigt, auf dessen Drehachse ein Potentiometer die Schieberposition bzw. den Lastzustand signalisiert.
Auf der Auslaßseite sind die Krümmer der Serie (Grauguß) durch einen in den Rohrlängen genau abgestimmten geschweißten Stahlrohrkrümmer aus warmfesten Werkstoff ersetzt. Wie beim Serienmotor werden die Zylinder 1+2+3 und 4+5+6 jeweils in ein Rohr zusammengeführt.
Um die Abgaswerte in einem vom Reglement definierten Meßpunkt und die Geräuschvorschriften zu erfüllen, werden die Abgasrohre in einen Katalysator und dann durch zwei Absorptionsschalldämpfer geführt.
Vorschrift lt. Reglement:
Abgas: n = 5000 U/min ( ohne Last) CO = 0,5 Vol.-% (+0,2 Vol.-% Meßtoleranz)
Geräusch = ONS-Nahfeldmessung 98 dB(A) +2 dB(A) Toleranz
Der Katalysator erhöht den Abgasgegendruck und mindert somit die Leistung. Die Unterschiede für die Abgasanlage mit und ohne Katalysator zeigt das folgende Bild:
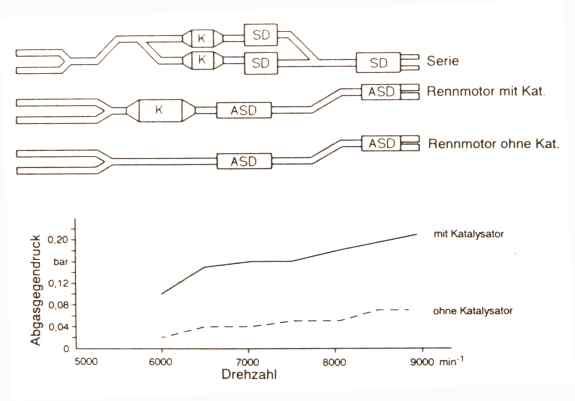
Zum Einsatz kommt die BOSCH Rennmotronic M 1.8, diese Anlage regelt Zündung und Einspritzung zylinderselektiv bis zu höchsten Drehzahlen. Fünfzehn parallel arbeitende Rechner im Steuergerät sorgen für die nötige Schnelligkeit. Pro Zylinder werden zwei Einspritzventile mit last- und drehzahlabhängigen unterschiedlichen Öffnungszeiten betrieben.
Im Gegensatz zum Serienmotor, der mit einem Zündverteiler ausgerüstet ist, hat der Rennmotor eine ruhende Hochspannungsverteilung. Die Zylinder-1.-Erkennung befindet sich an der Stelle des bisherigen Zündverteilers. Drehzahlinformation und O.T.-Position werden an der dafür günstigsten Stelle, dem Schwungrad, abgenommen.
Die Leistungsentwicklung wurde in 3 Phasen geplant:
Phase 1 : 265 kW bei 8000 U/min war im Februar 1990 abgeschlossen. Die Leistung wurde mit dem ersten Prototyp erreicht.
Phase 2 : 295 kW bei 8600 U/min wurde im August 1990 erreicht.
Phase 3 : etwa 310 kW bei 9200 U/min lief seit Anfang 1991 und wurde bald fertiggestellt.
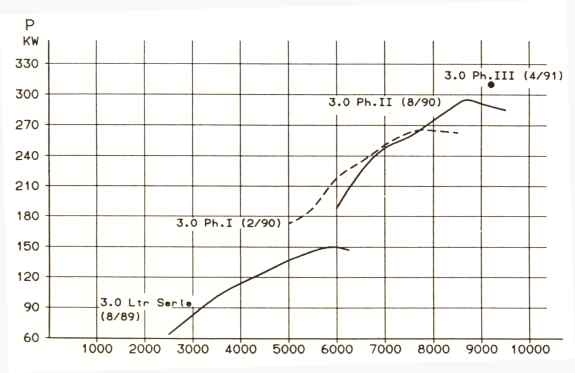
Schon bei der Entwicklung des OPEL-Sechszylinder-Vierventilmotors für den Omega 3000-24V wurde ein späterer Renneinsatz nicht ausgeschlossen. Die günstigen Voraussetzungen des Basismotors, auch im Hinblick auf extrem hohe Literleistung, bestätigten sich während der Entwicklung zum Rennmotor. Es wurde besonders auf den Kurbeltrieb geachtet, um die für den Rennbetrieb notwendigen hohen Drehzahlen bis 10 000 U/min realisieren zu können. Nach bisherigen Erkenntnissen scheint mit dem Leistungsziel Phase 3, d.h. 310 kW das Leistungspotenzial immer noch nicht ganz ausgeschöpft zu sein.
Artikel aus der MZT, Ausgabe 52 von 1991 Alle Urheberrechte bei den Verfassern Verfasser: Prof. Dr.-Ing. Fritz Indra Dipl.-Ing. Manfred Tholl Senator-Monza.de